Value Driven Adoption of AM Technologies
Tools and Methods for the focused adoption of additive manufacturing technologies in industry
Additive manufacturing technologies have been demonstrated to be feasible for applications in series products, and to enable substantial advantages in terms of achieving unprecedented design complexity and flexibility in manufacturing. Despite its readiness for direct manufacturing purposes, companies still face major challenges for successful and timely adoption of AM. Hence, implementation projects require many resources, lots of experimentation and show a high risk to not meet the expected outcomes. The efforts toward implementation can be drastically reduced if AM is implemented in a focused manner and in areas where it shows high potential for value creation.
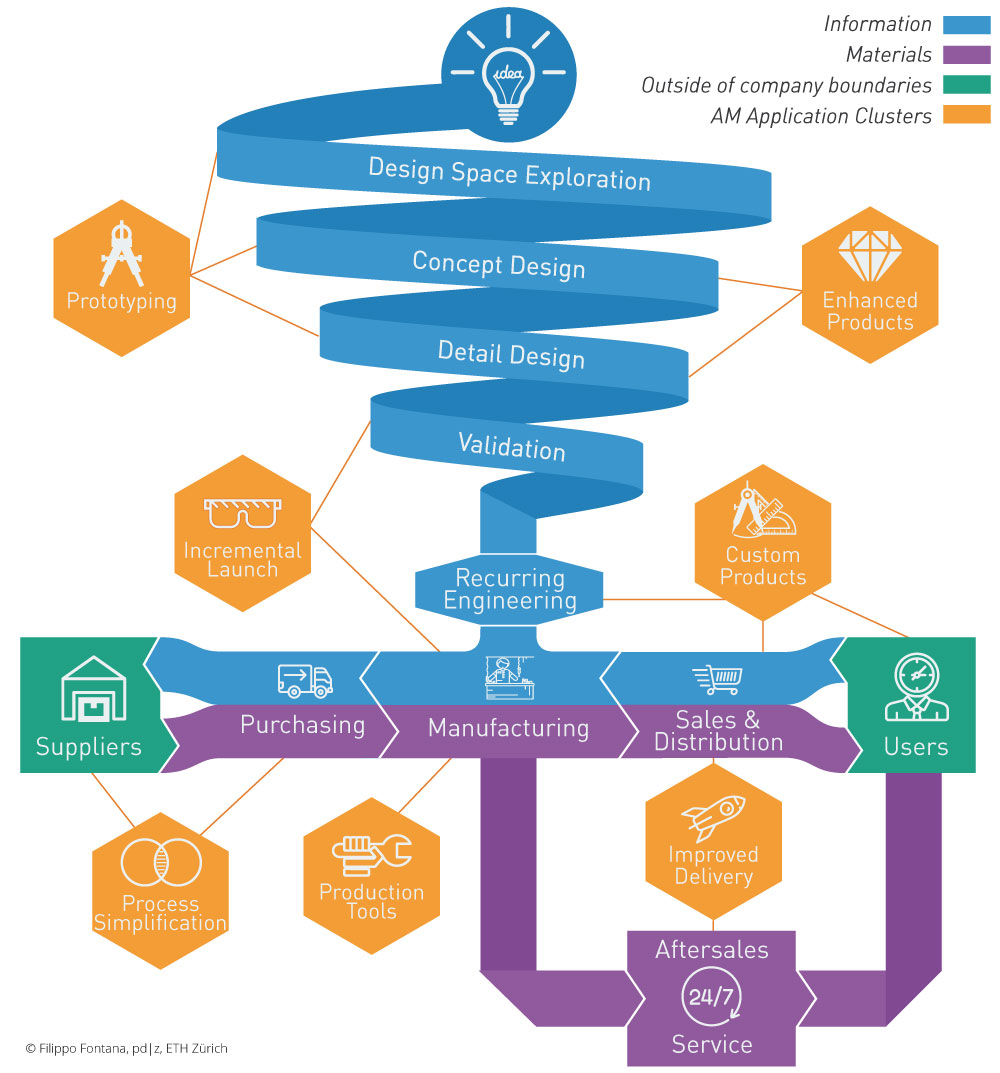
To address this issue our research aims at developing tools and methods to increase the likelihood of success of AM implementation projects. Our research is driven by the four following questions:
- Where in a firm value chain can AM be adopted to create unprecedented value?
- What are the benefits of implementation and what implications exist for established surrounding processes?
- How should companies structure the implementation process to accelerate AM adoption?
In a first stage our research developed a map of possible domains in a firm value chain where AM can be employed to create value for both the adopting company and the customer. This approach enables for a systematic screening of potential application domains of AM. Furthermore, by leveraging the defined clusters, the implementation resources can be focused on a single, clear defined area of interest, and therefore increase the efficiency of the implementation project. In a second stage the research closely observed some industrial implementation projects of AM to obtain valuable insights about the implications of adoption. In the novel field of Incremental product launch, defined by a close combination of AM technologies with agile development techniques for the purpose of accelerating, and mitigating the risks new product launches, we are currently running a CTI project in collaboration with ths swiss camera manufacturer ALPA.. The project aims at a better understanding of the incremental product launch phenomenon in its natural context, and at the development of guidelines for its application in an industrial setting.
In our research we apply empirical methods, based on the observation and close collaboration with early AM adopting companies. For qualitative analyses, we perform observations of state of the art AM applications to deduce information about value adding AM application clusters. We also perform quantitative analysis by fostering direct collaborations with Swiss pioneering SMEs in AM adoption.
Further Insights
-
ALPA 12 FPS ADD|METRIC custom solution with stiffening SLS manufactured cage to eliminate backlash between lens and sansor, and therefore enable high precision photogrammetric applications. -
First version of the SLS manufactured cage for the H6D100c digital back in the platon system. The cage integrates a power supply solution. -
PLATON full assembly. A compact system for large format cinematography. AM enables for a economic manufacturing of small lot sizes and for the possibility of constantly improving the product and its usability. The camera was designed by using the incremental product launch approach. -
Schematic representation of the incremental product launch approach. Major challenges are found in the domains of NPD, Operations and Customer relations. -
Schematics of a custom design solution for the Fusion360 CAD system. The plug-in allows for the direct ordering of parts at an approved supplier, and provides live cost estimation in CAD for different process chain combinations. The workflows is fully integrated with suppliers. The plugin reduces the efforts required by engineers to order parts in development, and helps in reducing manufacturing errors at the supplier errors.
For more information please contact Julian Ferchow.