Design Automation as an Enabler for Additive Manufacturing
Additive manufacturing offers nearly limitless design freedom. However, the manual design of complex parts is often time-consuming and challenging. In a recent doctoral thesis, we present novel algorithms to automate the design of flow components.
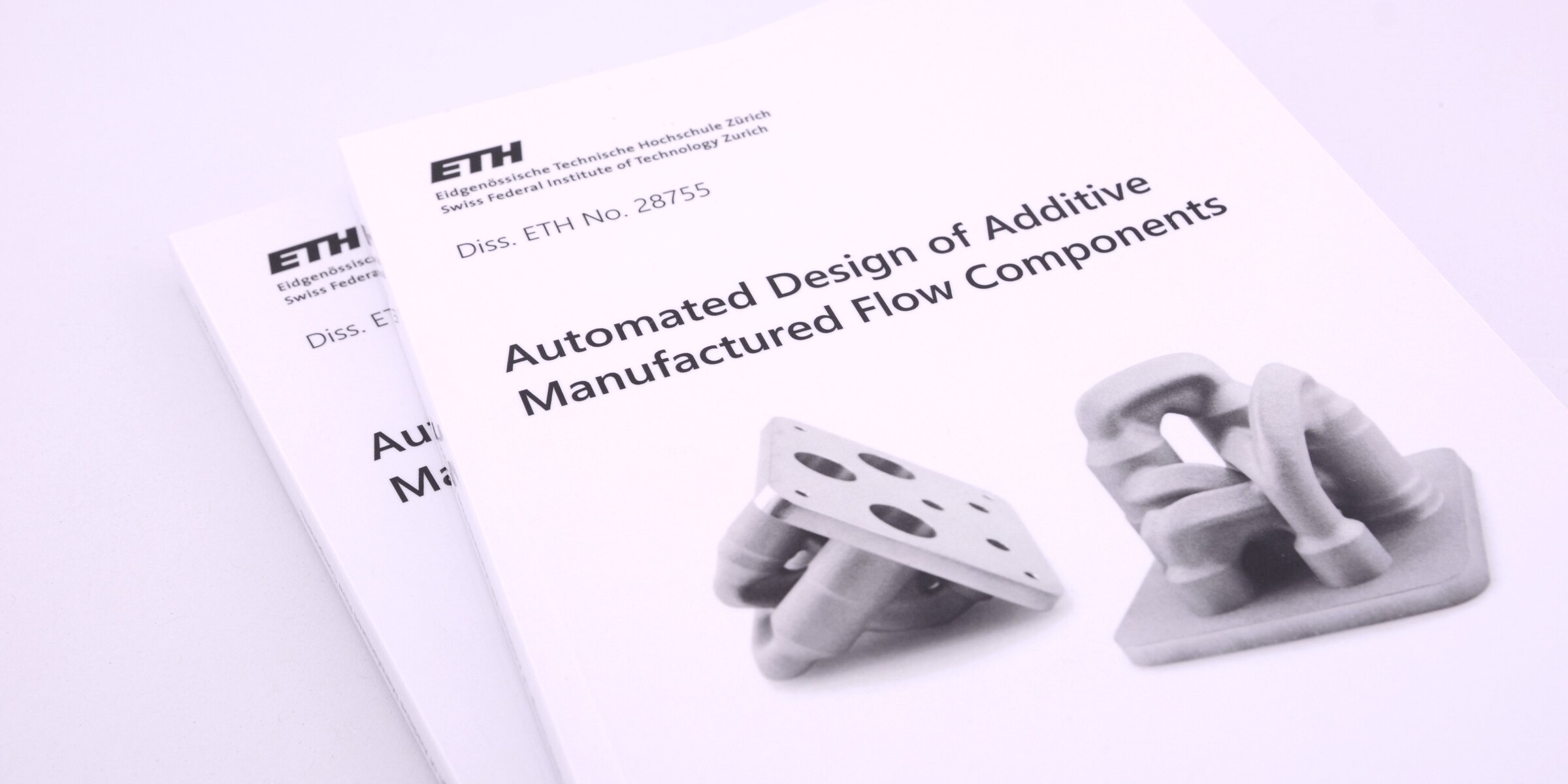
Many prior works highlight the potential of additive manufacturing (AM) for fluid flow components, such as nozzles, hydraulic manifolds, and heat exchangers. Compared to conventional manufacturing methods, such as milling and drilling, AM allows the fabrication of complex-shaped and functionally optimized flow structures. However, despite the potential of AM, a key challenge is to manually design such parts for AM, especially for novice users of computer-aided design (CAD) tools.
In a recent doctoral thesis, we present novel algorithms that enable the automated design of complex fluid flow components produced using AM. These design algorithms are developed to capture and integrate the application-specific knowledge required to generate the design of AM flow components, such as nozzles and manifolds. Furthermore, the algorithms automatically consider production-related restrictions of AM, such as the overhang constraint, adaption of channel cross-sections, and the use of integrated and sacrificial support structures.
The first part of the doctoral thesis focuses on the automated design of multi-flow nozzles. As shown in the figure, CAD users specify basic inputs such as the position and shape of different inlets and outlets. Based on this high-level definition, design algorithms translate the basic layout of a multi-flow nozzle into a detailed 3D geometry. The study demonstrates the workflow by showing the automated design of different nozzles that are tested using co-extrusion of clay materials. In addition, the research shows the transfer to industrial applications such as the co-extrusion of multi-layer polymer profiles.
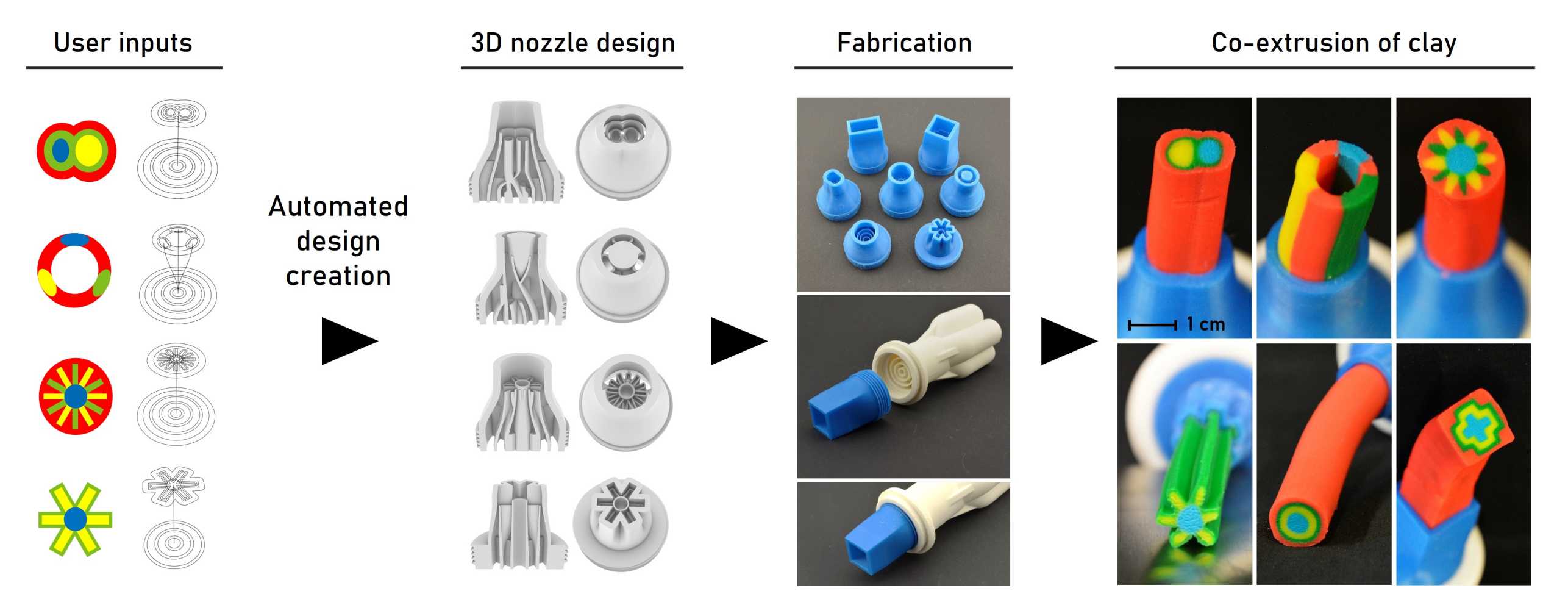
The second part of the doctoral thesis focuses on the automated design of hydraulic manifolds. Again, the basic idea is that CAD users only specify top-level user inputs. These inputs include functional requirements (e.g., inlets and outlets of channels, channel dimensions) and restrictions of AM (e.g., build direction, minimum build angle). Based on these inputs, design algorithms are used to automate the routing of multiple flow channels for separate fluid flows while considering the adaption of channel cross-sections to fulfill the AM overhang restriction. The final output is a detailed and production-ready 3D part geometry that can be used for simulations or the fabrication of prototypes.

The doctoral thesis Automated Design of Additive Manufactured Flow Components is available for download under this Link.
Further details on our research on design automation for additive manufacturing can be found here: Design Automation for Additive Manufacturing
For more information, please contact Manuel Biedermann