Design Automation for Advanced Manufacturing Technologies
Advanced manufacturing technologies such as Metal Additive Manufacturing have the large potential to enable new products and applications. However, to fully exploit their potential and apply them in value-adding applications, several challenges must be tackled, such as understanding the process characteristics and the related considerations in the design process.
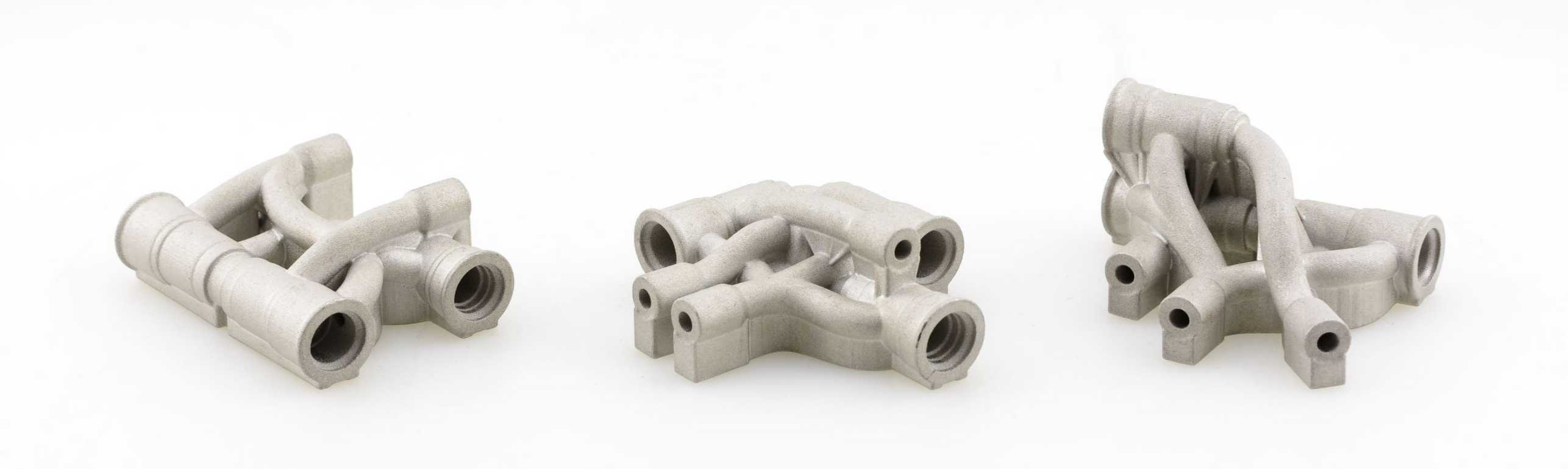
Understanding design-related aspects of the Metal Binder Jetting process
One such advanced manufacturing technology is Metal Binder Jetting (BJT-MSt/M, MBJ). It has recently emerged as a cost-effective alternative to the more established Laser Powder Bed Fusion (PBF-LB/M, LPBF) process. The main benefits are support-free manufacturing, batch production, and material versatility. However, the required sintering process poses challenges, as sintering distortion occurs when parts are not designed considering the inherent process characteristics. One field of research focuses on understanding the design-related aspects of the MBJ process to educate designers, enabling widespread industrial adoption of the process.
Investigating compensation strategies to reduce sintering-induced deformation
There are several approaches to address sintering-induced deformation. Firstly, part designs can be adapted manually based on an in-depth process understanding, reducing the amount and size of critical features, thereby reducing the sintering-related distortion and improving the part quality. This approach is, where applicable, a good first step to improve the outcome based on a well-thought-out design. However, some distortion will most likely remain, even on designs that adhere to the general design guidelines. These can be addressed with computational compensation strategies. Two main strategies exist: Firstly, an iterative simulation-based compensation where alternating sintering simulations and compensation steps are performed on the part design. The second approach is based on manufacturing the design, 3D scanning the resulting part, and using this scan as an input to the compensation procedure. In one research project, these compensation strategies are investigated on simplified geometries, compared regarding their effectiveness, and conclusions are drawn for the use on real part geometries.
Transfer to applications and industry
Based on the in-depth understanding of the process characteristics and strategies to handle sintering-induced deformation, these learnings can be transferred to industrial applications. In one specific project, the process-specific characteristics were implemented in a design tool for the automated design of fluid components. By implementing these design rules, a further manufacturing technology can now be chosen next to the LPBF process, enabling the user to choose the most adequate manufacturing technology depending on the application-specific requirements, lot size, and cost.
For more information please contact Urs Hofmann or Julian Ferchow.