Design Automation for Fluidic Applications
Fluid components such as manifolds or nozzles have the task of guiding, dosing, or regulating fluids from an inlet to one or multiple outlets. These tasks are central to many industrial applications and therefore represent a broad application. Design automation (DA) tools offer the opportunity to develop such components more efficiently and improve their performance. Therefore, in our research we develop DA algorithms to automatically generate technical designs for fluidic applications.
Design Automation for Milled Fluid Components
Most fluid components are produced using milling and drilling processes. These processes are well established, and the technical design follows a given pattern. During the design process, fluid components such as pumps, connectors and valves are spatially placed, and the flow channels are connecting ports using drilled holes. The flow channels are limited to linear guiding due to the manufacturing technology. The realization of more complex routes requires technical boreholes, which are closed again after milling. A good fluid manifold is therefore requiring as few boreholes as possible, takes only short boreholes, does not need technical boreholes and consumes a minimum volume of raw material. A reduction in the cost of such a block can therefore be realized by shortening the machining time, reducing the number of special tools and reducing the amount of raw material.
These parameters can be optimized in the engineering design process to generate an efficient design. This is where a design automation algorithm comes in, which is currently being developed. The aim of the algorithm is that a block can be generated widely automatically, enabling the creation of alternative designs in a short time to create the basis for optimization. The algorithm takes the information from a fluid circuit diagram as an input for generating the design. The used fluid components (e.g. valves, pumps) are imported from a library and arranged on the block. Simultaneously, the channels are routed from inlet to outlet considering all limitations coming from the milling process. A STEP geometry is generated as output, which can then be used in a CAM software for production planning.
Design Automation for Additive Manufactured Fluid Components
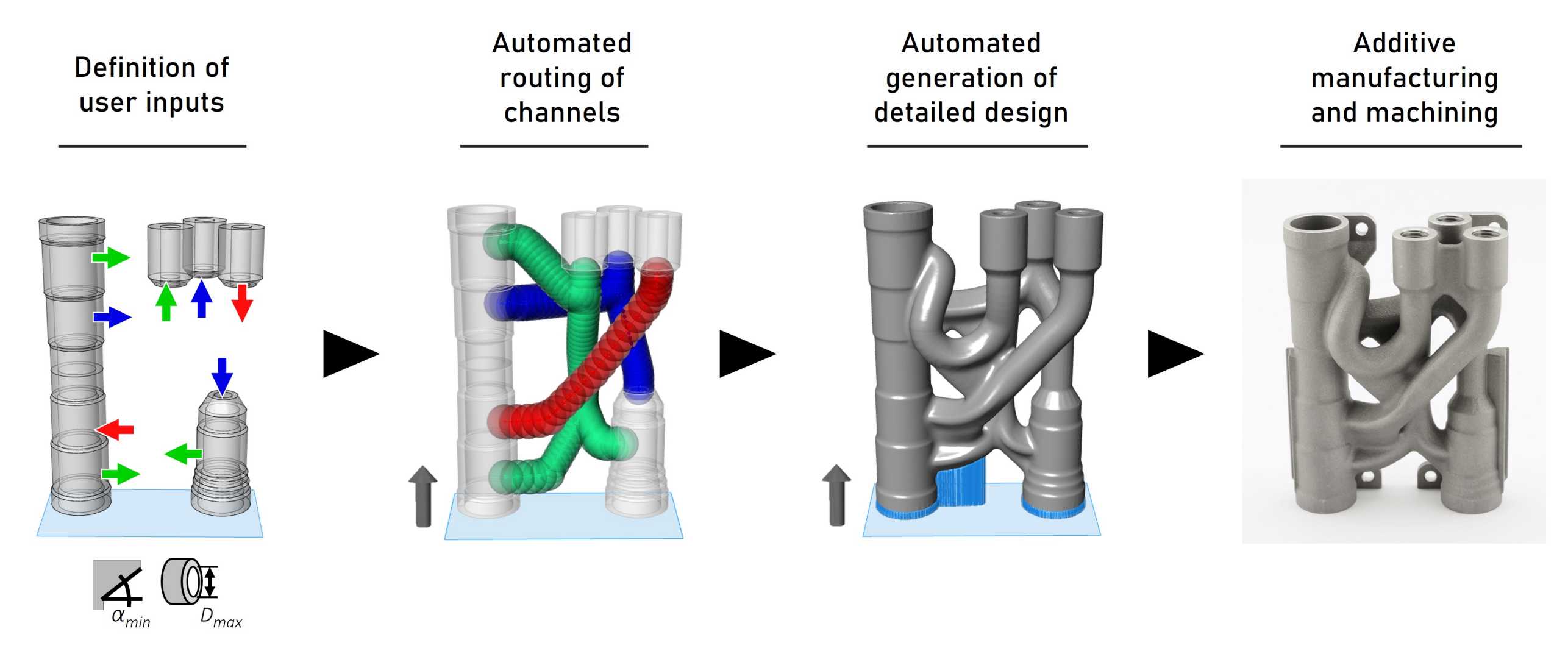
Additive Manufacturing processes offer the possibility of producing complex geometries without additional special tooling. This design freedom can be used in additively manufactured components to create fluid channels with continuously smooth centerlines. The great potential in additively manufactured fluid blocks lies in the reduction of pressure losses in flow channels, reduction of the overall weight, reduction of build size, and improvement in cleanability from process fluid. A challenging step in the development process is the creation of the technical design. As the design freedom of AM should be exploited, these channels should be optimized and consider AM design restrictions. The design time required for an AM component can therefore be multiple times higher than for a milled component.
For this reason, we have developed a design automation workflow that automates several steps of the development process. The workflow is composed of several modules that perform specific tasks in the overall process: (a) automated import of fluid components from a library and use of geometric information such as connection positions and interface geometries [publication submitted]; (b) automated creation of centerlines of fluid channels with smooth channel courses, considering other channels to avoid collisions external page [1]; and (c) automated generation of AM manufacturable fluid channels, with locally adapted cross-sectional geometry depending on the overhang to obtain self-supporting channels external page [2].
For more information please contact Patrick Beutler or Julian Ferchow.